ESSENTIAL EQUIPMENT FOR APPLYING COATINGS
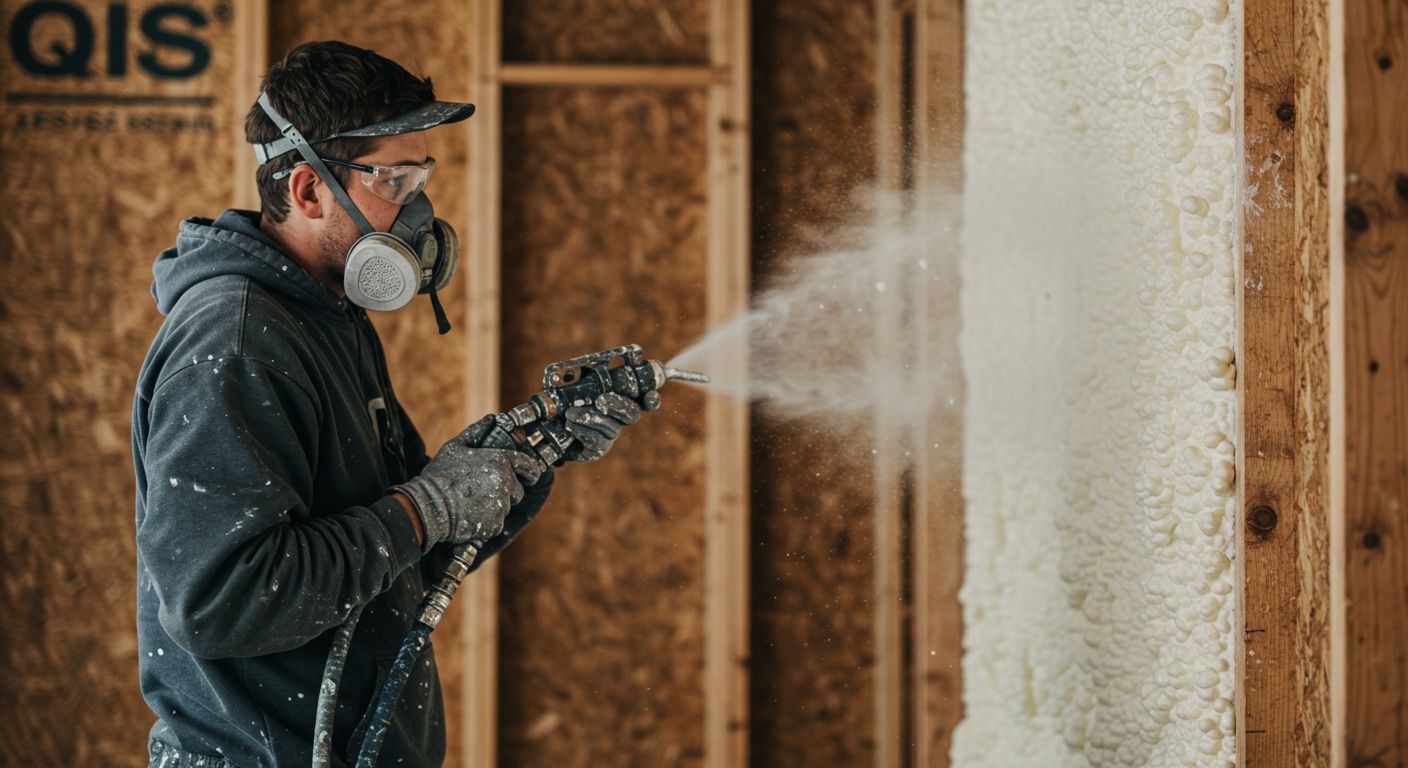
The application of protective coatings requires specialized equipment to ensure precision, efficiency, and safety. Below is an overview of the essential tools and machinery used in various protective coating processes.
1. Reactor Systems
Reactor systems are advanced pieces of equipment specifically designed for applications such as Spraywall and closed-cell spray foam. These hydraulic, heated, plural-component proportions offer exceptional performance and reliability. Key features include:
- Precision Heating and Mixing: Ensures the accurate blending of materials for optimal performance.
- High-Pressure Spray Capability: Facilitates even application over complex surfaces, delivering consistent results.
- Advanced Control Systems: Includes user-friendly interfaces and monitoring capabilities for precise adjustments and operational efficiency.
- Durable Construction: Built to withstand industrial conditions, ensuring long-lasting performance.
Applications: Ideal for waterproofing, insulation, and protective coatings in industrial and commercial settings, where precision and efficiency are critical.
2. Airless Spray Equipment
Airless spray equipment is widely used for applying protective coatings due to its high efficiency and uniform application. Key components include:
- Airless Spray Gun: Dispenses coating material at high pressure for smooth, even coverage.
- Pump System: Ensures consistent material flow, often powered by electricity, hydraulics, or pneumatics.
- Hoses and Nozzles: Connect the pump to the spray gun and control the spray pattern.
Applications: Ideal for large surfaces such as tanks, pipelines, and industrial structures.
3. Conventional Spray Guns
Conventional spray guns use compressed air to atomize and apply coatings. While less efficient than airless systems, they provide excellent control and finish quality.
Applications: Suitable for smaller or detailed projects requiring a finer finish.
4. Electrostatic Spray Equipment
Electrostatic spray systems charge the coating particles, which are then attracted to the grounded surface. This technique minimizes overspray and ensures even coating.
Applications: Commonly used for metal surfaces, machinery, and automotive parts.
5. Brushes and Rollers
Traditional brushes and rollers remain vital tools for:
- Touch-up work
- Small areas
- Applying thicker coatings or primers
Applications: Used in areas with limited access or where precision is required.
6. Surface Preparation Equipment
Proper surface preparation is critical for coating adhesion and longevity. Common equipment includes:
- Sandblasters: Remove rust, old paint, and debris using high-pressure abrasive material.
- Power Washers: Clean surfaces with water or chemical solutions.
- Grinders and Sanders: Smooth and prepare surfaces before coating.
Applications: Preparing steel, concrete, or wood surfaces for coating application.
7. Mixing and Agitation Tools
To ensure a consistent application, coating materials often require thorough mixing. Essential tools include:
- Mechanical Mixers: Blend coatings to achieve uniform viscosity and composition.
- Paddle Mixers: Simple tools for small-scale mixing tasks.
Applications: Preparing epoxy, polyurethane, or multi-component coatings.
8. PPE (Personal Protective Equipment)
Safety is paramount in protective coating applications. Workers require:
- Respirators: Protect against inhalation of harmful fumes and particulates.
- Gloves and Protective Suits: Shield skin from chemicals and abrasive materials.
- Goggles and Face Shields: Provide eye and face protection during spraying and surface preparation.
Applications: Mandatory in all coating and surface preparation processes.
9. Curing and Drying Equipment
Proper curing ensures the durability and effectiveness of coatings. Equipment includes:
- Heat Lamps and Ovens: Speed up the drying process in controlled environments.
- Dehumidifiers and Ventilation Systems: Maintain optimal humidity and airflow.
Applications: Critical for epoxy and other coatings that require specific curing conditions.
10. Inspection and Quality Control Tools
To ensure the coating meets industry standards, inspection tools are essential, such as:
- Thickness Gauges: Measure the coating’s dry film thickness.
- Adhesion Testers: Assess the bonding strength of the coating.
- Humidity and Temperature Monitors: Ensure environmental conditions are suitable for application and curing.
Applications: Used throughout the coating process to maintain quality and compliance.
Conclusion
The application of protective coatings requires a combination of advanced equipment and meticulous preparation. By using the right tools, businesses can achieve durable, high-quality results that protect their assets and meet industry standards. At QISBC, we provide comprehensive coating solutions using state-of-the-art equipment and techniques. Contact us to learn more about how we can meet your protective coating needs.