U-Haul coating project
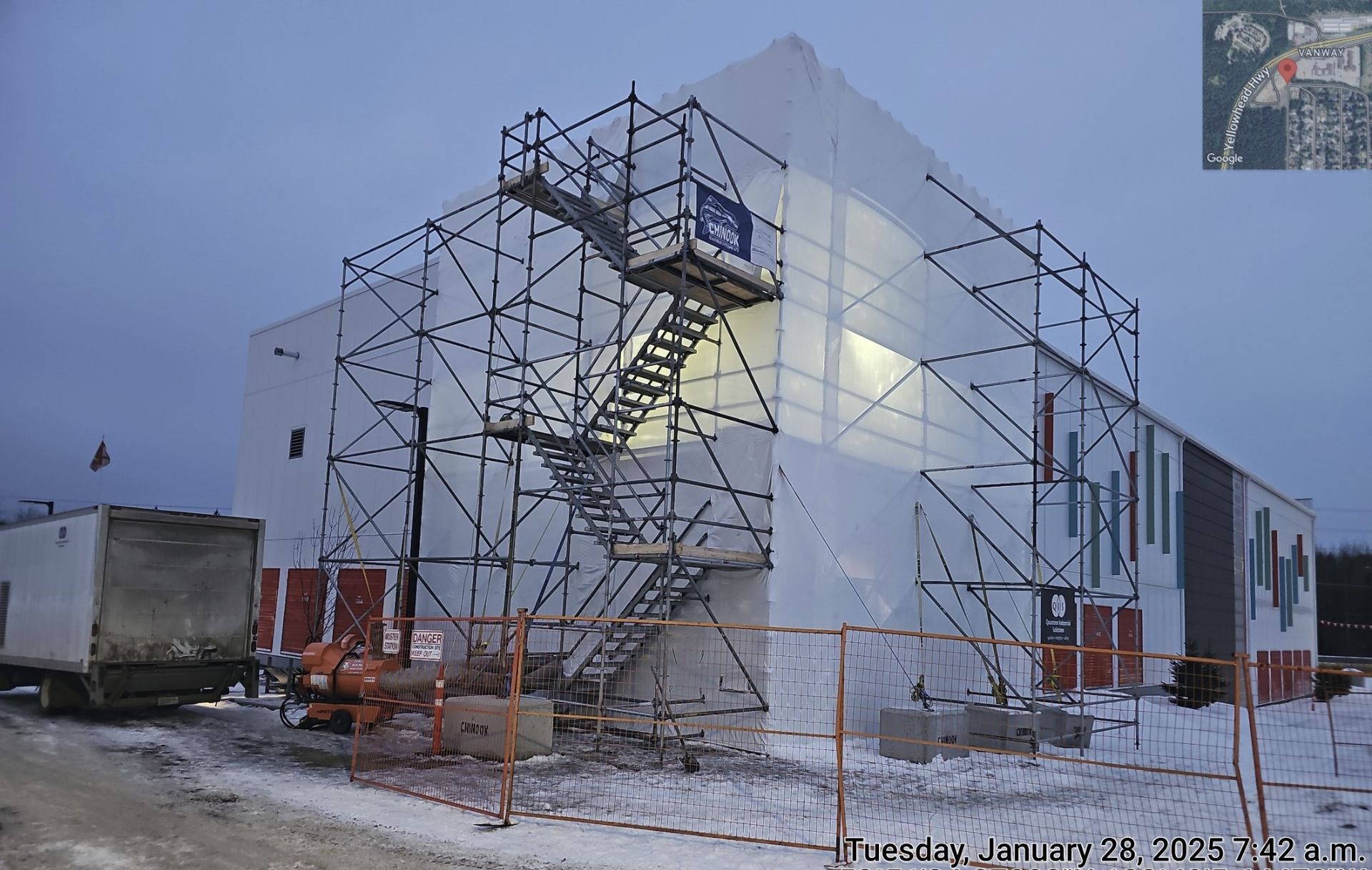
Ensuring Perfection: The U-Haul Project in Extreme Conditions
At QISBC, we take pride in tackling complex industrial coating projects that demand precision, expertise, and resilience. Our recent U-Haul project (240100) was a true test of our capabilities, pushing our team to operate in extreme winter conditions while maintaining the highest industry standards.
Project Overview
This project involved the application of Coraflon® ADS Epoxy PVDF Bonding Primer and Coraflon® ADS Intermix Topcoat on sensitive project bodies requiring meticulous surface preparation, strict adherence to Inspection Test Plans (ITPs), and high-level quality control. Given the nature of the project, a NACE Level 3 inspector was on standby throughout the process to ensure compliance with specifications.
Challenges Faced
1. Extreme Cold Weather (-20°C) and Hoarding
One of the biggest hurdles was the subzero temperatures, which made it impossible to apply coatings without proper environmental controls. To combat this, we installed hoarding around the work area and deployed three 400,000 BTU/h heaters at each site, ensuring a stable environment for surface preparation and coating application.
2. Specialized Paint Requiring Precise Handling
The PVDF-coated surfaces demanded a specific preparation process, including solvent cleaning, fine-grit sanding (220–400 grit), and strict surface profile requirements (1.0 mil minimum). Any deviation could compromise adhesion and durability, requiring constant monitoring and corrective actions.
3. Meeting Exacting Quality Standards
With highly sensitive project components, every step was rigorously inspected to meet industry standards:
Surface preparation inspections ensured all defects, contaminants, and gloss removal were properly addressed.
Environmental condition checks confirmed the correct temperature, humidity, and dew point margins.
Wet Film Thickness (WFT) and Dry Film Thickness (DFT) measurements were conducted per ASTM and SSPC PA2 standards to ensure consistency.
NACE Level 3 oversight guaranteed compliance with coating specifications and ITP requirements.
4. Maintaining Workflow Efficiency Under Strict Protocols
The client required an exact routine based on the ITP, meaning there was zero margin for deviation. This required real-time documentation of inspections, material usage, and process adherence. Any unexpected variations were promptly addressed to maintain quality and consistency.
Results and Takeaways
Despite the challenges, the Bedrock U-Haul project was completed successfully, with coatings applied to the highest standards of durability, adhesion, and aesthetic quality. The combination of advanced environmental controls, meticulous application techniques, and strict quality assurance ensured the final product met and exceeded expectations.
This project highlights QISBC's ability to execute high-precision coating applications under extreme conditions, reinforcing our reputation as a leader in industrial coatings.
If you’re looking for a reliable partner for high-performance coatings in challenging environments, contact us today!
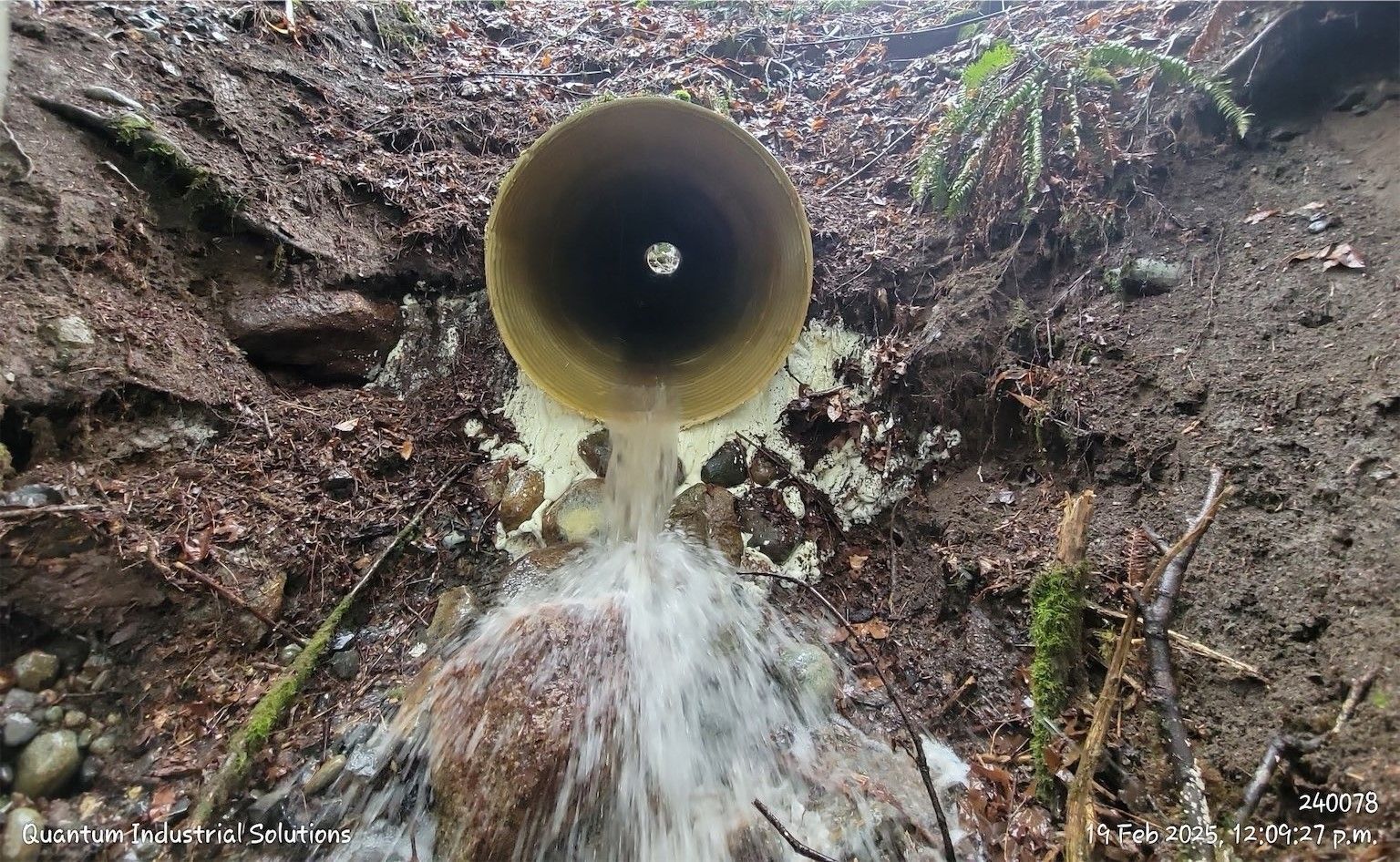
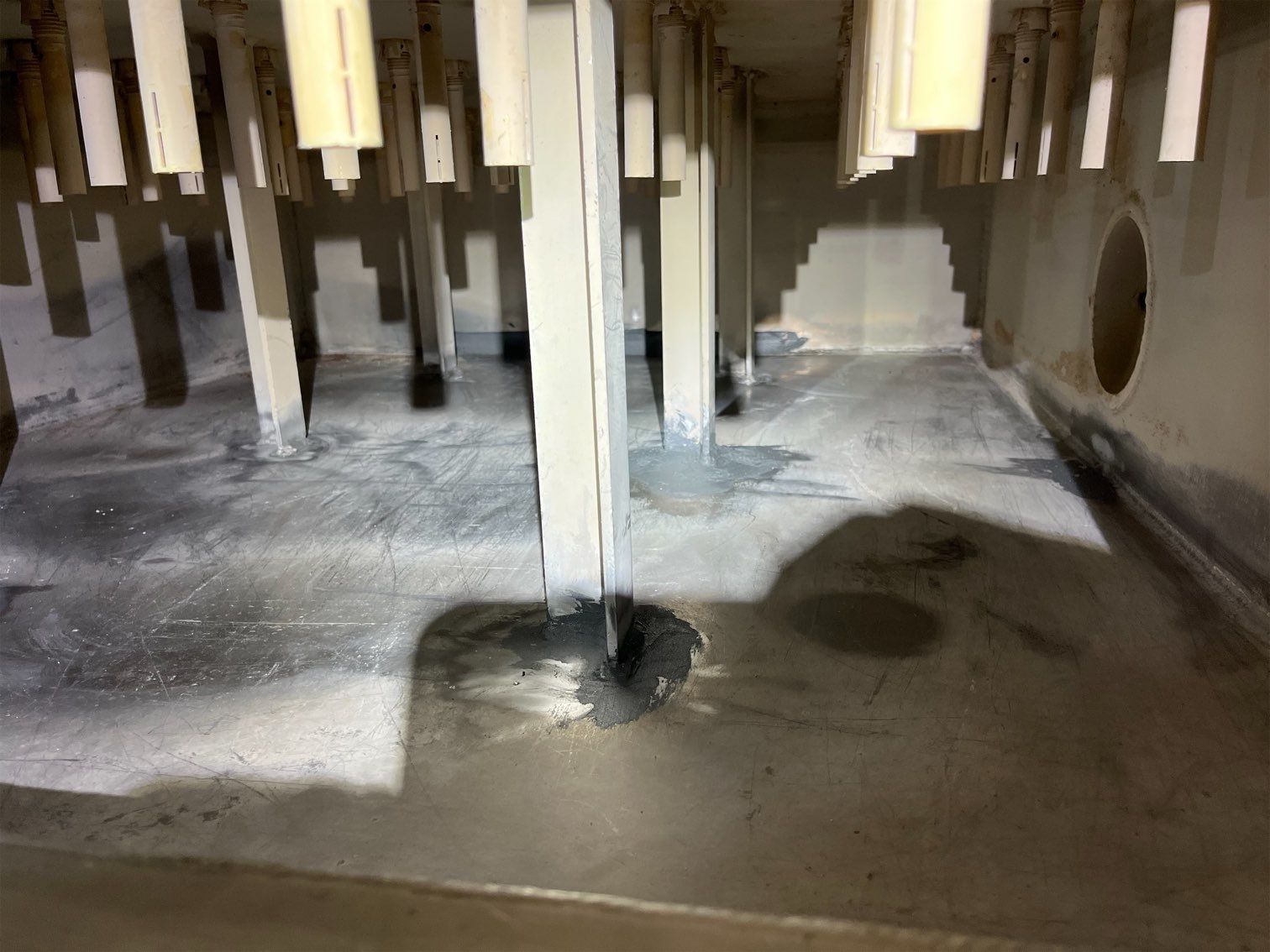
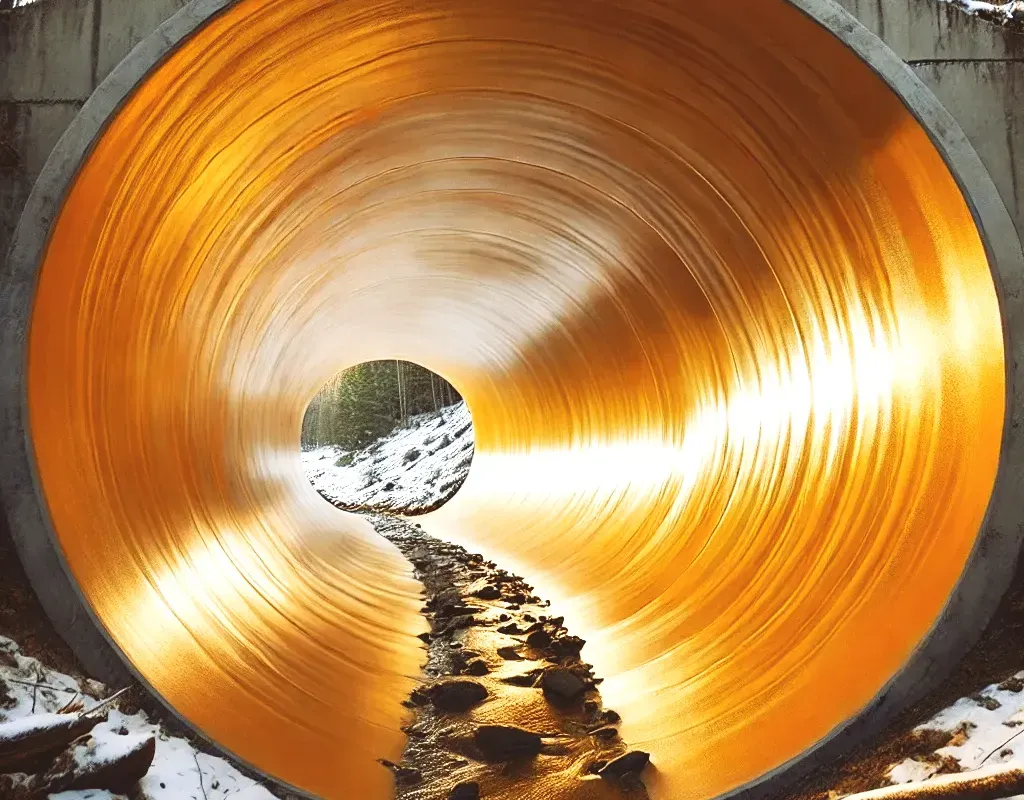
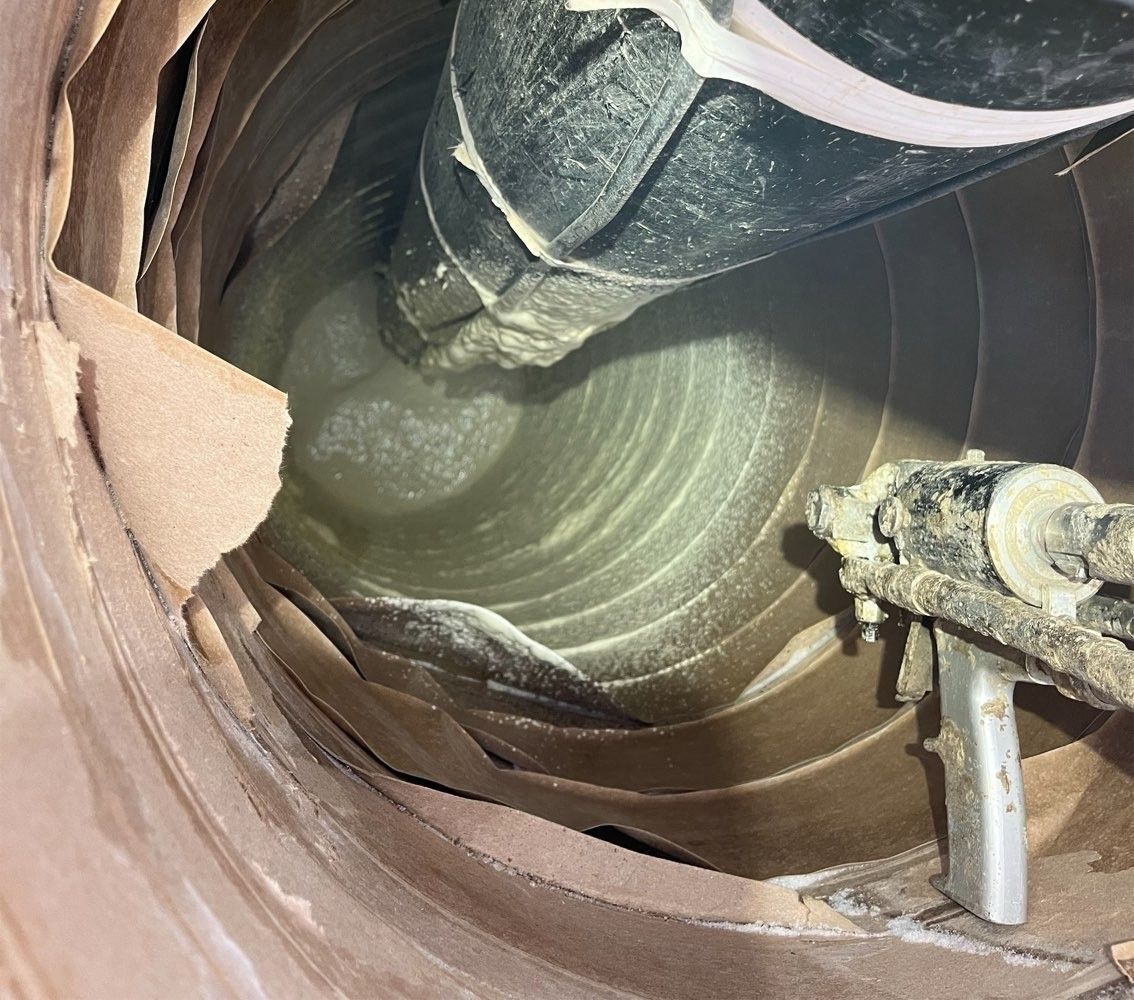
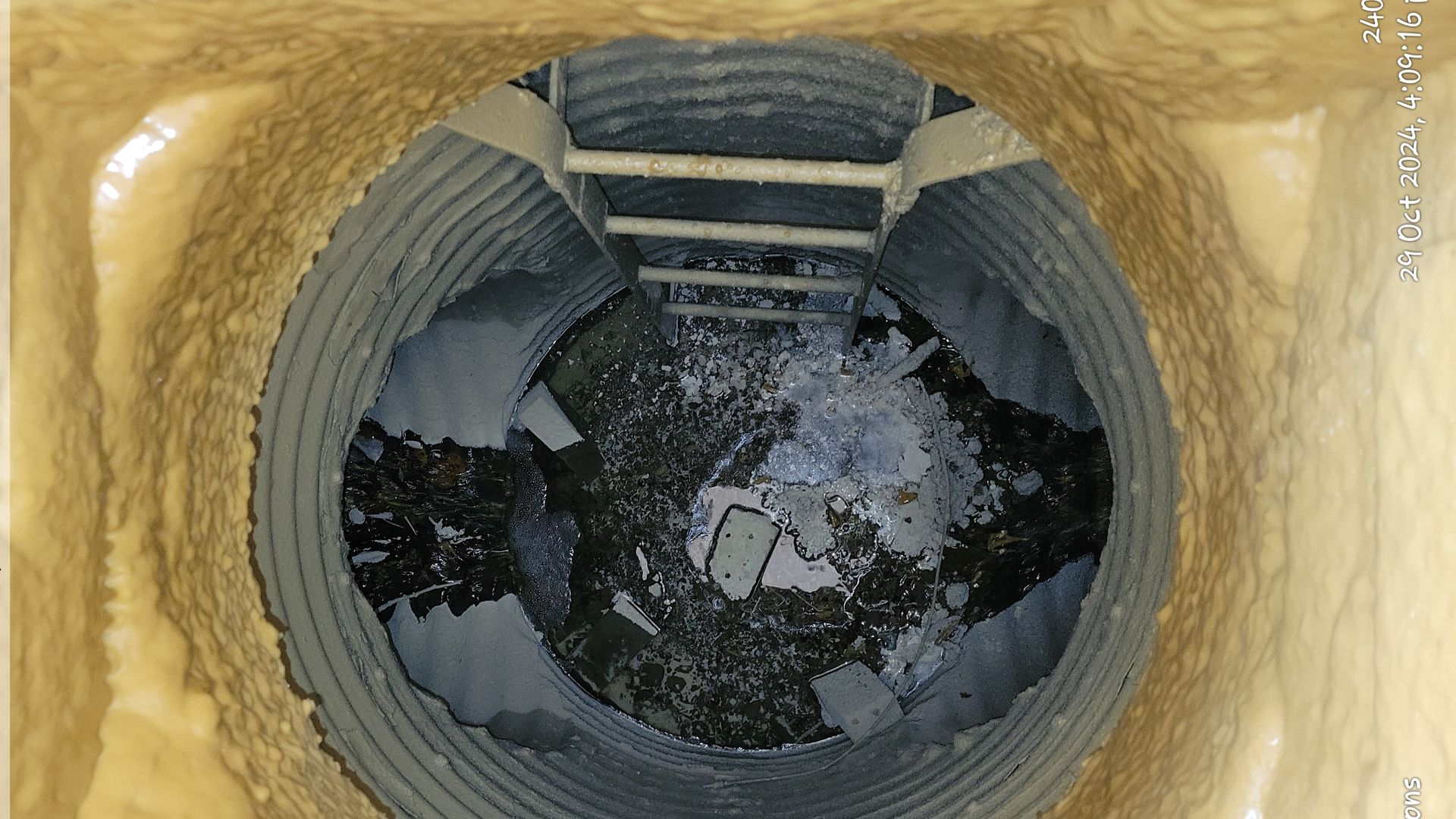
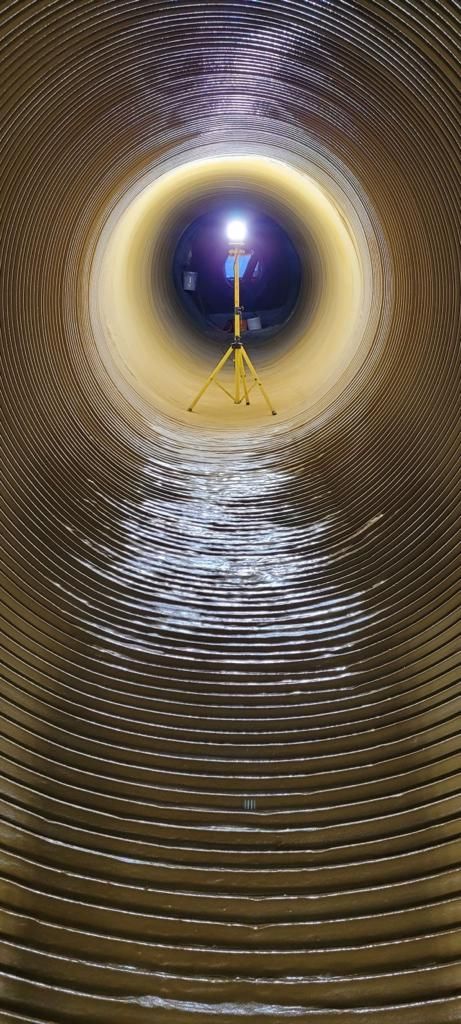